If cash flow is the life blood of a business then inventory is the oxygen that flows through the lungs of the business. Too little oxygen and the business will die. Too much oxygen and it will die.
Inventory, or stock as we used to call it, is seen as source of waste under the Lean rules but in the modern unpredictable business environment that is too simple a view.
Inventory is often associated with stuff piled high in warehouses and is seen as the complete opposite of the desire for the ‘efficient’ technique of Just In Time. This policy may be efficient but is it effective?
Businesses have become allergic to inventory as their customers will not pay for it and so it is seen as waste. The cry of let’s take x% out of inventory before we publish the year end figures resonates around the land.
In recent years we have seen how poorly thought out so many supply chains really are. Even as I write this two production facilities (one at Mini and one at Porsche) are shut down due to the breakdown of their supply chain as a result of the war in Ukraine. Covid and Brexit have caused untold problems due to supply chain failures mostly based on the poorly thought out rush for cheap is best.
Even leaving aside the supply chain disasters it is too simple to look at inventory as one item. We need to consider at least three divisions and then each stock keeping unit within each.
Raw Materials
Without raw materials a manufacturing business is dead. Without the raw input for their services a service provider is dead. As stated in my last blog one of the rules of Just In Time is that you have your suppliers close to you. Modern supply chain methods have suppliers spread all over the world and this is not Just in Time. Today we see the error of pretending that this is efficient. If you are going to employ this sort of supply chain strategy then holding raw material inventory is essential. The time has come to properly evaluate the true cost of low bought in production versus the cost of disruption in an increasingly unpredictable world.
In the service industry it is the same. If you are providing a service you must have the raw materials to answer the need of the customer. This is one of the reasons we have increasingly seen the rise of insurance companies providing domestic services to landlords and householders who in return for a premium expect jobs to be done immediately and are not prepared to wait for parts.
Likewise, the increasing use of cloud services means our stock of data under our control is getting less and less. Maybe an accessible stock of back ups should be considered. For many businesses data is their raw material.
Work In Progress
This is the most dangerous type of inventory. The problem is made worse by the fact that accounting principles state that work in progress is worth more than raw materials. As a product gains value as it moves through production we attribute cost and hence ‘value’ to it. The truth is often the exact opposite. Raw materials can usually be sold, finished goods can usually be sold but how much would you pay for a part complete sofa or an aeroplane with no wings? Probably less than the basic raw materials.
The opposite is the case in the service industry. Here WIP is often not valued. In an order processing area or graphic designers much time may well have been invested but a part-finished document or brochure actually has negative value. If the estate agent for whom I have produced the brochure goes under I may well have to pay to have the brochures taken away and destroyed. A fast movement through the WIP stage is essential for both manufacturers and services.
It is in the area of Work In Progress where we should concentrate our efforts. Low WIP done correctly can massively increase both the efficiency and effectiveness of the business, not to mention productivity.
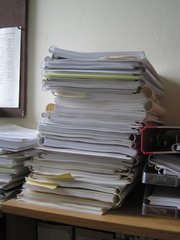
This is WIP in the same way as that on the shop floor and probably has a greater detrimental effect on your business.
Finished Goods
The rise of online shopping for both personal and business goods and services and particularly the success of companies such as Amazon has changed the game with regard to finished goods.
Increasingly the customer will not wait. Unless you are providing a bespoke product or service then finished goods are a necessity. Demand based processes are the ideal and nobody wants a warehouse full of unsold finished goods – or do they?
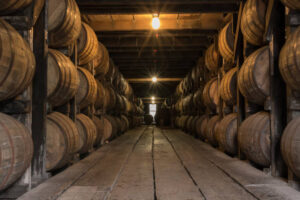
Sometimes the longer you keep the finished goods the more valuable it becomes. Don’t go for a fast stockturn ratio here!!
In the modern business environment we may need to think about inventory in a different manner. Having the correct level at the the correct stage is where our efforts should be concentrated. The correct level is not necessarily the lowest. Simplistic ideas of just taking a percentage out of inventory to increase efficiency are definitely not the way to increase effectiveness.
The correct use of techniques to eliminate the true areas of waste in inventory have never been so important but the correct holding of the most effective levels of inventory may well be the difference between success and failure.
If you want to look at this further we have both manufacturing and service simulations to enable staff to be trained to evaluate the most effective way of dealing with inventory – particularly WIP. Please contact us for details.
If you want to look at this further we have both manufacturing and service simulations to enable everyone to be more effective. Please contact us for details – https://www.wellsassoc.co.uk/contact/.
If you want to be kept up to date with blogs and other matters please subscribe to our newsletter – http://www.wellsassoc.co.uk.
Analogy From The Bee Hive
When supplies are easily accessible bees store up sufficient stocks to see them through unpredictable times. If supplies suddenly become unavailable the lack of raw materials does not stop production in the hive. In modern times with unpredictable supply chain problems we should note this effective policy.